Have you ever wondered how your favorite brochure, magazine, or packaging gets printed so perfectly? Behind every colorful page or sharp label, there’s a detailed process that takes place in a printing press.
Even though the world is going digital, printing is still a big part of our everyday life —from posters on the wall to cartons on supermarket shelves. Knowing how the printing press process works can help you understand what goes into making high-quality print products.
In this article, we’ll explain the entire process step by step, from preparing the design to the final printed product. We’ll also look at different types of printing, like offset and digital printing, what machines are used, and which method is better for your needs.
Whether you’re running a print business, thinking of buying a machine, or just curious, this guide will give you a clear picture of how professional printing works—in simple words.
Let’s begin!
What Is a Printing Press?
A printing press is a machine that puts text and images onto paper or other materials. It’s used to create things like newspapers, books, posters, packaging, brochures, and labels. Whether you’re printing one copy or thousands, the printing press makes it fast, accurate, and cost-effective.
The first printing press was invented by Johannes Gutenberg in the 1400s. That changed the world—it made books more available and helped spread knowledge quickly. Today, printing presses are much more advanced and automated, but the goal is still the same: to transfer ink onto paper in a clean, clear, and professional way.
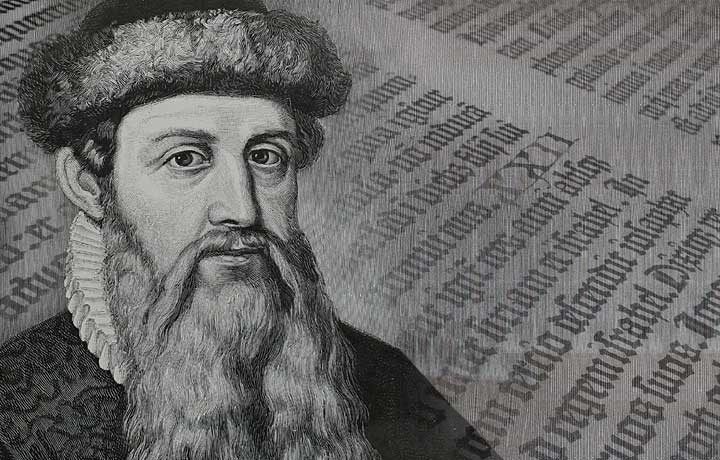
There are two main types of printing presses used today:
- Offset Printing Press – Best for large quantities with top print quality (like magazines, packaging, catalogs).
- Digital Printing Press – Ideal for short runs or personalized jobs (like invitations, business cards, flyers).
No matter the type, every printing press follows a series of steps—from getting the design ready to deliver the final printed sheets.
Types of Printing Processes
There are different ways to print depending on what you’re making, how many copies you need, and what materials you’re printing on. From short-run flyers to high-volume packaging, each printing method has its own strengths. Let’s explore the most common types of printing processes used in the printing industry today:
1. Offset Printing
Offset printing is the most widely used method for large-scale printing. It uses metal plates to transfer ink onto a rubber blanket, which then prints the image onto paper. This method offers excellent color consistency and sharp details, making it ideal for long runs.
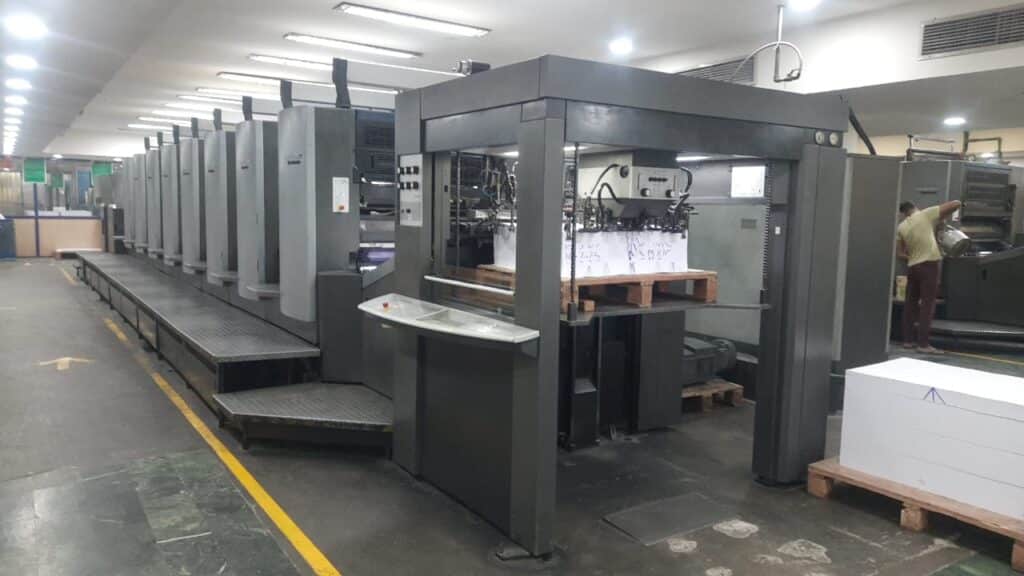
Best For: Magazines, brochures, books, cartons
Why Choose It: High quality, cost-effective for bulk printing.
2. Digital Printing
Digital printing doesn’t use plates. It prints directly from a digital file, like a PDF, straight onto the paper. This process is fast and perfect for short runs or personalized printing jobs, such as business cards or flyers with variable data (like names or QR codes).
Best For: Small batches, personalized printing, quick jobs
Why Choose It: No setup plates, faster turnaround, affordable for low-volume
3. Flexographic Printing (Flexo)
Flexography is mostly used for packaging. It uses flexible rubber or polymer plates and can print on various materials like plastic, foil, and cardboard. It’s fast and works well for printing large quantities of labels and wrappers.
Best For: Labels, flexible packaging, plastic pouches
Why Choose It: Fast, handles different materials, great for packaging
4. Gravure Printing
Gravure printing uses engraved cylinders and is perfect for extremely high-volume and high-quality printing. It’s commonly used for magazines, wallpaper, and some packaging products.
Best For: Catalogs, high-end packaging, large runs
Why Choose It: Superb detail and image depth for large-scale work
5. Screen Printing
Screen printing is a traditional method where ink is pushed through a mesh screen onto the surface. It’s best for custom jobs on fabric or flat surfaces. This method is slower but great for specialty printing.
Best For: T-shirts, tote bags, posters, signage
Why Choose It: Great for thick inks, bold colors, and textured prints
6. Letterpress Printing
Letterpress is one of the oldest printing methods. It presses inked text or images into paper to create a slightly debossed, textured effect. Today, it’s mainly used for premium print items like wedding invitations or art prints.
Best For: Invitations, cards, artisan prints
Why Choose It: Beautiful craftsmanship and a tactile, elegant feel
Printing Process Comparison Table
Printing Type | Best For | Quantity Range | Highlights |
---|---|---|---|
Offset Printing | Brochures, books, packaging | High Volume | Best quality for large runs |
Digital Printing | Flyers, cards, personalized items | Low to Medium | Fast and affordable for short runs |
Flexography | Labels, pouches, packaging | Very High Volume | Prints on many surfaces |
Gravure Printing | Magazines, high-end packaging | Massive Volume | Rich detail, fast production |
Screen Printing | Clothing, signage, specialty products | Low to Medium | Bold colors and custom designs |
Letterpress Printing | Invitations, luxury prints | Custom/Small Batch | Brochures, books, and packaging |
How the Printing Press Process Works
Now that you know the different types of printing, let’s break down how the printing press process works. Whether it’s a large-scale offset printing machine or a smaller digital printer, the steps are quite similar. Here’s what happens from start to finish:
1. Prepress – Getting Ready to Print
The first step is called prepress. This is where the design files (usually in PDF format) are checked and prepared for printing. The process includes:
- Checking image quality and resolution
- Making sure colors are in CMYK (used for printing)
- Adding crop marks and bleed areas
- For offset: creating metal printing plates for each color
- For digital: loading the file into the press software
This step ensures that everything prints correctly and with good quality.
2. Plate Making (Offset Only)
In offset printing, metal plates are made for each color—Cyan, Magenta, Yellow, and Black (CMYK). These plates carry the image that will be transferred to paper.
Each plate is mounted on the press, and the image is first transferred to a rubber blanket, then onto the paper—this is why it’s called “offset.”
This step doesn’t apply to digital printing, since it prints directly from a file.
3. Setup and Calibration
Before the real printing starts, the press operator does some setup:
- Loads the paper
- Aligns the plates (in offset)
- Calibrates ink levels
- Adjusts the registration (to make sure all colors line up)
- Runs a few test sheets to check for any errors
This is a key part of the commercial printing process, ensuring everything looks sharp and clean.
4. Printing
Now comes the main part: printing the job.
- In offset printing, the machine pulls sheets of paper and applies the ink through the plates and rollers.
- In digital printing, the file is printed directly using toner or inkjet technology.
The press can print thousands of sheets per hour, depending on the job and machine. Larger machines even have features like automatic ink control, sheet alignment, and non-stop feeders for smoother operation.
5. Drying
Once the ink is applied, it needs to dry before finishing. Drying methods depend on the type of press:
- Offset printing often uses IR dryers, UV lamps, or just air drying.
- Digital printing usually dries instantly with heat or toner fusing.
This step ensures the print doesn’t smudge or stick during the next stages.
6. Finishing
After printing, the sheets go through finishing processes like:
- Cutting
- Folding
- Binding (for books and catalogs)
- Laminating or coating (for protection or shine)
- Punching, embossing, or die-cutting (for packaging or creative jobs)
Finishing turns flat prints into final products like brochures, cartons, or magazines.
7. Quality Check & Delivery
Before delivery, each job goes through a quality control check. The team looks for color consistency, alignment, and any print defects. Once approved, the job is packed and shipped or handed over to the client.
Step-by-Step Printing Press Process Summary Table
Step | What Happens | Applies To |
---|---|---|
Prepress | File setup, CMYK conversion, plate making | Offset & Digital |
Plate Making | Cutting, folding, binding, and lamination | Offset Only |
Setup | Paper loading, color calibration | Offset & Digital |
Printing | Ink/toner applied to paper | Offset & Digital |
Drying | IR/UV/Air drying or toner fusion | Offset & Digital |
Finishing | Cutting, folding, binding, lamination | Offset & Digital |
Quality Check | Final inspection before delivery | Offset & Digital |
Why Offset Printing Still Matters Today
Even with the rise of digital printing, offset printing remains the top choice for:
- High-volume printing
- High-quality images and colors
- Wide paper size options (like 28×40 inches)
- Cost efficiency for large batches
It’s widely used for printing magazines, posters, packaging, labels, and even newspapers.
The offset printing process is a powerful blend of technology, precision, and craftsmanship. It may seem complex, but it’s designed for one purpose: to deliver professional, consistent, high-quality results, job after job.
If you’re involved in the printing industry or planning a big print job, understanding how offset printing works can help you make smarter choices.
Now that you’ve seen the complete step-by-step printing press process, you can better understand how your designs turn into real, high-quality print materials.
Digital Printing Process Explained
Digital printing has changed the way we think about printing. Unlike traditional methods like offset printing, digital printing is fast, flexible, and ideal for smaller jobs. It doesn’t require printing plates, making it the go-to choice for short-run printing and customized jobs.
So, how does digital printing work? Let’s walk through the process step by step.
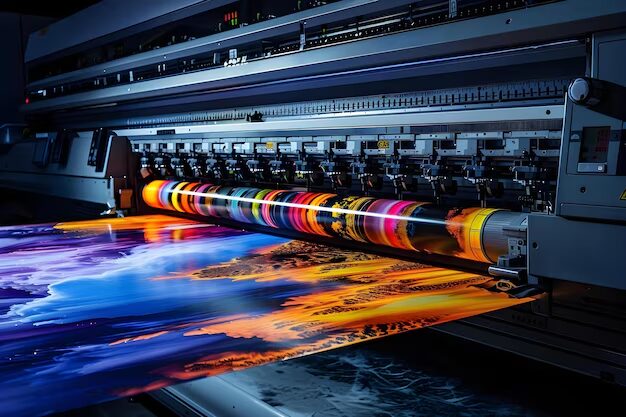
1. Design and File Preparation
Like any printing method, everything starts with the design. Once your brochure, flyer, business card, or label is ready, it is saved in a digital format—usually as a high-resolution PDF.
There’s no need to separate colors or create metal plates. The file is sent directly to the digital printing press. This saves time and cost, especially for smaller orders.
Common tasks at this stage include:
- Checking resolution (usually 300 DPI or more)
- Converting to CMYK color mode
- Adding bleed and crop marks
- Proofing the design digitally before the final print
2. Printing Begins (No Plates Needed)
Here’s where digital print technology stands out: it prints directly from the file onto paper, without using plates, blankets, or water. There are two main types of digital printing technologies:
- Laser Printing (Electrostatic / Toner-Based):
Uses a laser to create an image on a drum, which is then transferred using toner onto paper and fused using heat. - Inkjet Printing:
Uses tiny nozzles to spray ink directly onto the paper. Best for high-quality images, photographs, and posters.
Digital printers can handle a wide range of sizes and materials—coated paper, labels, cards, synthetic sheets, and more.
3. Ink or Toner Application
Unlike offset printing, where ink is transferred in layers, digital printing applies all colors in one pass. The machine uses CMYK toner or ink cartridges to recreate the image on the paper.
In high-end commercial digital presses, you might also find:
- Spot color options (for branding)
- White ink (for colored or transparent substrates)
- Varnish or clear coatings for extra shine
The digital printing process is extremely accurate and clean, making it ideal for detailed images and personalized content.
4. Fusing or Drying
In toner-based systems, heat is used to fuse the toner particles onto the paper. In inkjet systems, the ink dries quickly on the surface or is cured using UV light (in UV inkjet printers).
This step ensures the print is smudge-proof and ready for handling or finishing right away.
5. Finishing Touches
Once printed, sheets may go through finishing operations, such as:
- Cutting or trimming
- Folding
- Stapling or perfect binding (for booklets)
- Lamination or UV coating
- Creasing or perforating
Because digital printing is often used for on-demand jobs, the finishing process is quick and highly automated.
6. Variable Data Printing (Optional)
One of the best things about digital printing is variable data printing (VDP). This allows you to change specific parts of each print—like names, addresses, or QR codes—without stopping the press.
It’s perfect for:
- Direct mail campaigns
- Event Invitations
- Personalized marketing materials
This level of customization is not possible with offset printing unless you stop and reconfigure the setup for each copy.
Why Digital Printing Is Popular Today
The digital printing process is ideal for businesses and print shops that need:
- Fast turnaround times
- Low-volume orders
- On-demand printing
- High-quality results
- Personalization or data-driven marketing
It’s widely used in advertising, packaging, label printing, business stationery, and more.
Pros of Digital Printing
✅ No setup time
✅ No plates or chemicals
✅ Great for short runs
✅ Supports variable data
✅ Fast delivery
✅ Lower cost for small jobs
Limitations of Digital Printing
❌ Higher cost per page for large quantities
❌ Slightly lower color accuracy vs offset for certain jobs
❌ Limited substrate options compared to offset
❌ May lack specialty finishes (like embossing or metallic inks)
The digital printing process is all about speed, flexibility, and convenience. If you’re looking to print small batches, test marketing materials, or personalize each print, digital is the smart choice.
Thanks to rapid advances in technology, today’s digital presses are closing the quality gap with offset machines, and many businesses now use both depending on the job.
Machines Used in the Printing Process
The printing process involves more than just putting ink on paper. From pre-press to printing and finishing, various machines work together to create high-quality printed materials. Whether it’s a brochure, magazine, carton, or poster, each stage uses specific types of equipment. Let’s take a closer look at the most common machines used in the printing industry.
1. Offset Printing Press
Offset presses are the heart of traditional commercial printing. These machines use metal plates to transfer ink to a rubber blanket and then onto paper. They’re perfect for high-volume and high-quality printing.
Popular Models:
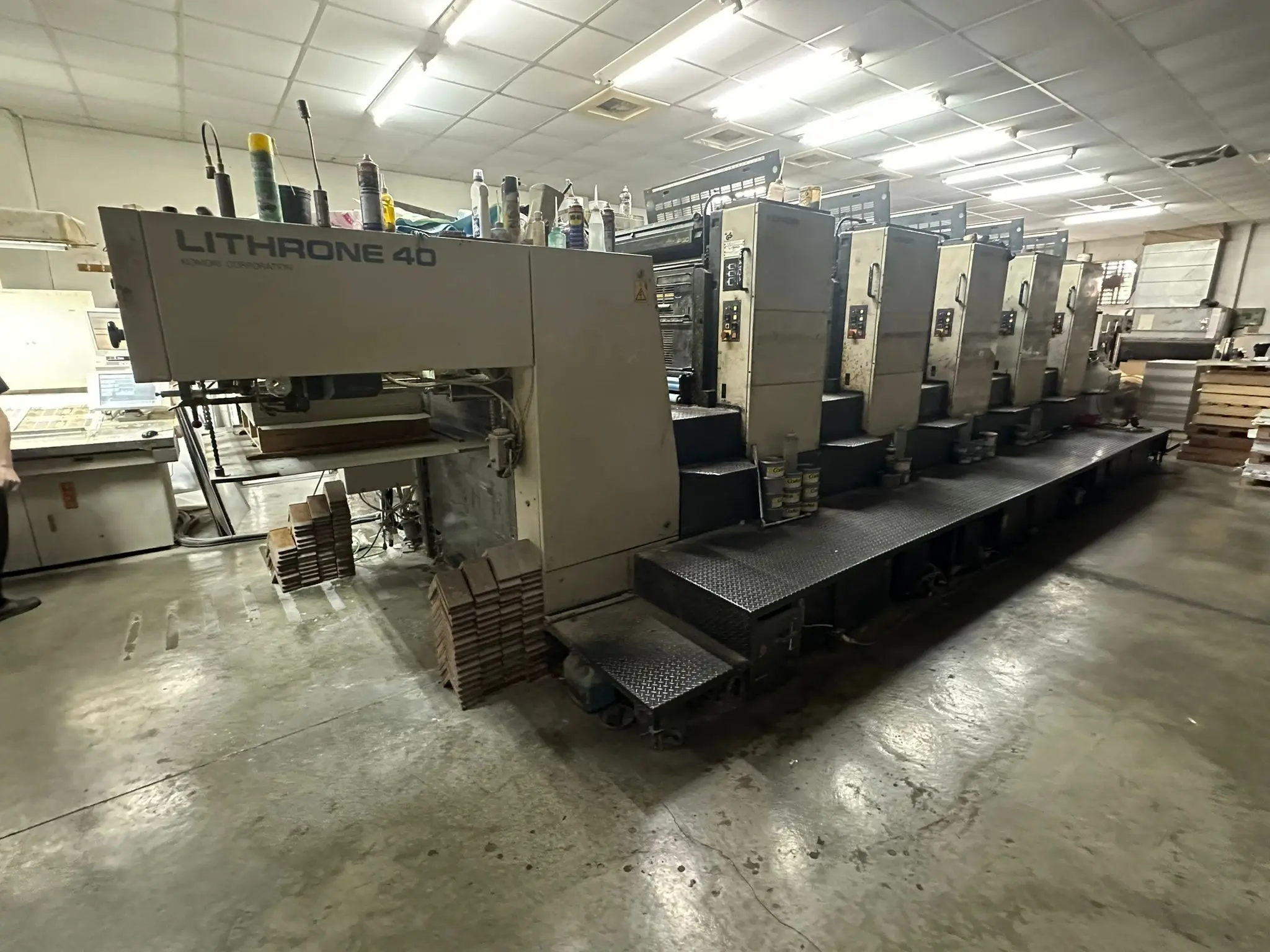
Key Features:
- 2 to 10 color units
- Sheet-fed or web-fed systems
- Precision ink control systems
- Automated plate changers and dryers
Offset presses are ideal for magazines, packaging, catalogs, and other mass print jobs.
2. Digital Printing Machine
Digital printers work directly from a digital file, without the need for plates. These machines are commonly used for short runs, fast delivery, and customized prints like business cards, flyers, and labels.
Types:
- Toner-based digital presses (e.g., Canon, Xerox, Ricoh)
- Inkjet printers (e.g., Epson, HP Indigo, Konica Minolta)
Key Features:
- Quick setup
- Variable data printing (for personalized jobs)
- High-speed output
- UV, dye, or pigment inks
These machines are ideal for small businesses and marketing agencies that need on-demand printing.
3. CTP Machine (Computer-to-Plate)
A CTP machine is used in the pre-press stage of offset printing. It takes your digital design and directly creates aluminum plates, eliminating the need for film or manual processes.
Why It’s Important:
- Speeds up plate-making
- Increases accuracy
- Saves labor and reduces errors
CTP is essential in offset printing setups.
4. Plate Punch and Bender
This machine helps align the plates accurately before they are mounted on the press. Without it, plates may misalign, affecting print registration.
Key Benefits:
- Ensures perfect alignment
- Saves setup time on the press
- Increases color accuracy
5. Folding Machines
Once the sheets are printed, many jobs need to be folded into brochures, flyers, or booklets. Folding machines do this automatically and quickly.
Types:
- Knife folders
- Parallel fold machines
- Combination folders
Used widely in commercial printing for high-speed folding.
6. Cutting Machines / Guillotines
After printing, sheets are often trimmed to their final size using guillotine cutting machines. These machines offer clean, sharp cuts, which are essential for a professional look.
Top Brands: Polar, Wohlenberg, Perfecta
Features: Hydraulic cutting, programmable controls, safety sensors
Cutting machines are a must-have for any print finishing department.
7. Laminating Machines
To add a protective and glossy finish, laminating machines apply a thin plastic film over printed sheets. This makes them water-resistant and durable.
Common Uses:
- Business cards
- Menus
- Book covers
- Packaging inserts
8. UV Coating Machines
UV coating machines apply a shiny or matte coating to enhance visual appeal and protect the print. A UV lamp instantly dries the coating.
Used for:
- Catalogs
- Magazines
- Product packaging
These are often used alongside UV printing machines.
9. Binding Machines
If you’re printing books, reports, or manuals, binding machines bring the pages together. There are many types:
- Perfect binding (softcover books)
- Saddle stitching (magazines)
- Wiro binding (notebooks)
Binding completes the final product and makes it ready for use or sale.
10. Die-Cutting Machines
For printing jobs that require custom shapes (like boxes or folders), die-cutting machines cut the sheets with high precision using steel dies.
Die cutting is used in:
- Packaging
- Stickers
- Custom invitations
It’s a crucial step in packaging and commercial print production.
The modern printing process is powered by a combination of smart, efficient, and high-precision machines. From the initial design to the final product, each machine plays a specific role to ensure speed, quality, and consistency.
Commonly Used Printing Machines:
- Offset printing presses (for bulk jobs)
- Digital printers (for fast, short-run work)
- CTP systems (for plate-making)
- Finishing equipment (for cutting, folding, laminating, and binding)
Whether you’re running a small print shop or a large commercial press, understanding the machines used in the printing process helps you choose the right equipment—and ultimately, deliver better results for your customers.
Common Materials Used in the Printing Press Process
The success of any printing job doesn’t just depend on machines and technology—it also relies heavily on the materials used in the printing process. From paper and ink to printing plates and chemicals, each material plays a vital role in ensuring high-quality, durable, and professional results.
Let’s explore the most commonly used printing materials that are essential in both offset and digital printing environments.
1. Paper
Paper is the most obvious and most important material used in printing. The type, thickness, texture, and coating of the paper can dramatically affect the final result. In commercial printing, paper is selected based on the type of job.
Common Paper Types:
- Coated Paper: Smooth and glossy or matte finish. Ideal for magazines, brochures, and catalogs.
- Uncoated Paper: Has a rougher texture, suitable for letterheads, books, and forms.
- Art Paper: High-quality coated paper used for luxury print jobs.
- Newsprint: Lightweight, uncoated paper used for newspapers.
- Cardstock: Thick paper used for business cards, packaging, and postcards.
- Synthetic Paper: Waterproof and tear-resistant, used for labels, outdoor signs, and manuals.
Sheet sizes can vary, but common formats include 20×29 inches, 23×31 inches, and 28×40 inches for offset printing.
2. Ink
Ink is the lifeblood of any print job. In traditional printing methods like offset printing, ink is applied in layers of CMYK (Cyan, Magenta, Yellow, and Black). In digital printing, ink or toner is directly applied to the surface.
Types of Ink Used in Printing Presses:
- Offset Ink: Oil-based ink used in sheet-fed offset presses. Comes in standard CMYK or special Pantone shades.
- UV Ink: Cures instantly under ultraviolet light. Used in both offset and digital UV printers.
- Soy-Based Ink: More eco-friendly and offers brighter colors than petroleum-based inks.
- Water-Based Ink: Commonly used in flexographic and packaging printing.
- Toner: Used in laser digital printers, not liquid ink but powdered pigment.
3. Printing Plates
Plates are used only in offset printing, not in digital printing. They carry the image to be printed and are usually made of aluminum.
- CTP Plates (Computer-to-Plate): Most modern printing uses these for precision and speed.
- Conventional Plates: Older method involving film exposure.
- Polyester Plates: A Cheaper alternative for short-run jobs, often used in small offset presses.
Each color in a job requires a separate plate.
4. Blankets
In offset printing, a rubber blanket transfers the image from the plate to the paper. These are wrapped around cylinders in the press.
- Rubber Blankets: Soft and flexible, helping print on textured or uneven surfaces.
- Compressible Blankets: Reduce dot gain and improve print sharpness.
Blankets must be cleaned regularly for best performance.
5. Chemicals and Solutions
The printing press requires several solutions to help manage ink and water balance, clean equipment and ensure smooth operation.
Common Chemicals Used:
- Fountain Solution: A mix of water and additives that keep non-image areas ink-free.
- Plate Cleaner: Used to clean and protect printing plates.
- Roller Wash & Blanket Wash: Solvents are used to clean rollers and blankets.
- Anti-set-off Powder: Applied between sheets to prevent smudging and sticking.
- Dampening Solution: Helps control ink flow and improve print consistency.
Many modern shops now use low-VOC (volatile organic compound) solutions to reduce environmental impact.
6. Printing Films (for Prepress)
While less common now due to digital workflows, some print shops still use transparent films for exposing plates, especially in screen or traditional flexographic printing.
- Positive Films: Show the image in black on a clear background.
- Negative Films: Reverse image, used in certain exposure methods.
7. Coating and Finishing Materials
After printing, many jobs go through finishing to enhance appearance and durability.
Common Finishing Materials:
- Varnish: Adds a shiny or matte layer to printed surfaces.
- Lamination Film: A Thin plastic layer applied for protection.
- UV Coating: Cured with UV light to create a glossy finish.
- Die-Cutting Dies: Used for shaping the paper (e.g., boxes or folders).
- Binding Glue: For perfect-bound books and catalogs.
8. Packaging and Label Substrates
In packaging and label printing, additional materials are used:
- Corrugated Board: For box printing and folding cartons.
- Vinyl and BOPP: For waterproof and weatherproof labels.
- Foil Paper: Used in luxury packaging and security printing.
The quality of a printing job is not just about the machine—it’s also about using the right materials for printing. From the type of paper to the kind of ink and even the cleaning chemicals used, each material contributes to the look, feel, and durability of the final product.
Key Materials in Printing:
- Paper (coated, uncoated, cardstock)
- Ink (CMYK, UV, soy-based)
- Printing plates and blankets
- Chemicals (fountain solution, cleaners)
- Finishing supplies (laminate, varnish, glue)
Understanding these printing press materials helps businesses choose the right combination for every job, whether it’s high-end packaging, business cards, or commercial brochures.
Quality Control in the Printing Process
In the world of printing, quality matters a lot. Whether you’re printing business cards, packaging, or catalogs, the final product must look sharp, clean, and consistent. That’s where quality control in the printing process plays a crucial role. It ensures that every sheet, label, or box that comes off the press meets your standards—and your client’s expectations.
Let’s break down how professional printers maintain top quality at every stage.
Why Quality Control Is Important in Printing
Poor print quality can lead to wasted materials, unhappy customers, and financial loss. Common issues like color mismatch, misregistration, smudges, and paper jams can ruin an entire batch.
Quality control in commercial printing helps prevent:
- Color inconsistencies
- Blurry images or text
- Ink smears or set-off
- Paper misfeeds or wrinkles
- Misaligned printing (registration errors)
- Incorrect finishing (cutting, folding, binding mistakes)
By following a careful quality control process, printers ensure that every job is accurate, clean, and professional.
Key Stages of Quality Control in Printing
1. Pre-Press Quality Checks
Before anything is printed, the pre-press stage is where files are prepared and checked.
Common pre-press checks:
- Are the files in high resolution (usually 300 DPI)?
- Is the color mode set to CMYK instead of RGB?
- Are bleed, trim, and safe zones properly added?
- Are fonts embedded and images linked?
- Are print marks (crop marks, registration marks) included?
Errors caught here can save a lot of time and money. Many print shops also run a soft proof or PDF proof for client approval before printing begins.
2. Plate and Ink Calibration (Offset Printing)
In offset printing, quality control includes making sure the plates, rollers, and ink settings are just right.
Key checks include:
- Plate alignment (registration) – Ensures all colors line up correctly
- Ink density levels – Prevents over- or under-inking
- Blanket cleanliness – Dirty blankets can cause ghosting or smudges
- Water-ink balance – Essential for clean, sharp prints
Some advanced presses use densitometers and spectrophotometers to measure color and ink levels accurately. This helps maintain color consistency throughout long runs.
3. On-Press Monitoring
During the print run, the press operator constantly monitors the output.
They look for:
- Color shifts or fading
- Blurry or distorted images
- Paper misfeeds
- Ink build-up or roller issues
- Print-to-print variation
Print inspection systems (manual or automated) help catch problems early. In many modern machines, PQC (Print Quality Control) consoles allow real-time adjustments of ink flow, registration, and sheet alignment.
4. Post-Press Quality Checks
After printing is done, the job moves to the finishing stage—cutting, folding, binding, or laminating. Errors here can ruin a perfectly printed job.
Post-press quality control involves:
- Checking if cuts are clean and aligned
- Verifying correct page order in bound books
- Making sure folds are straight and accurate
- Ensuring lamination is bubble-free and sealed
- Inspecting glued edges or stitched areas for strength
Each final product is usually sample-checked by hand or scanned by machines for flaws.
5. Final Inspection and Packaging
Before shipping to the client, a final inspection is done to ensure everything meets the agreed specifications.
This includes:
- Comparing printed samples to the proof
- Checking color against Pantone or approved swatches
- Confirming quantity and size
- Looking for scratches, smudges, or paper tears
- Ensuring correct packing for transport
Many commercial printers also include a QC checklist with the shipment for traceability and customer confidence.
Tools and Techniques Used in Print Quality Control
- Densitometers – Measure ink density on paper
- Spectrophotometers – Analyze color accuracy
- Loupe/Magnifiers – Inspect fine print details
- Color Bars and Control Strips – Printed along with jobs to help monitor ink balance
- Automated print inspection systems – Scan every sheet at high speed
Best Practices for Print Quality Control
✅ Always calibrate your machines regularly
✅ Train operators to spot issues early
✅ Use standard quality control charts (like ISO or G7 standards)
✅ Keep clean working conditions to avoid dust or contamination
✅ Communicate clearly with clients about expectations and proofs
✅ Maintain maintenance logs for equipment and quality tracking
Quality control in the printing process is what separates an average job from a professional one. From file preparation and ink calibration to on-press monitoring and post-print inspection, every step plays a role in making sure your print work looks its best.
Whether you run an offset press or a digital printer, focusing on print accuracy, color consistency, and defect prevention builds trust with clients and helps grow your business.
Applications of the Printing Press Process
The printing press has completely transformed the way we share, sell, and store information. From magazines to packaging, the impact of printing is all around us. With modern offset and digital technologies, the printing press process has become faster, sharper, and more flexible than ever before.
Let’s look at the most common and practical applications of printing press machines in today’s world, especially in the commercial printing and packaging industries.
1. Commercial Printing
One of the largest uses of printing presses is for commercial printing. This includes producing everyday marketing materials, business documents, and more.
Examples:
- Brochures
- Flyers
- Business cards
- Posters
- Letterheads
- Presentation folders
- Annual reports
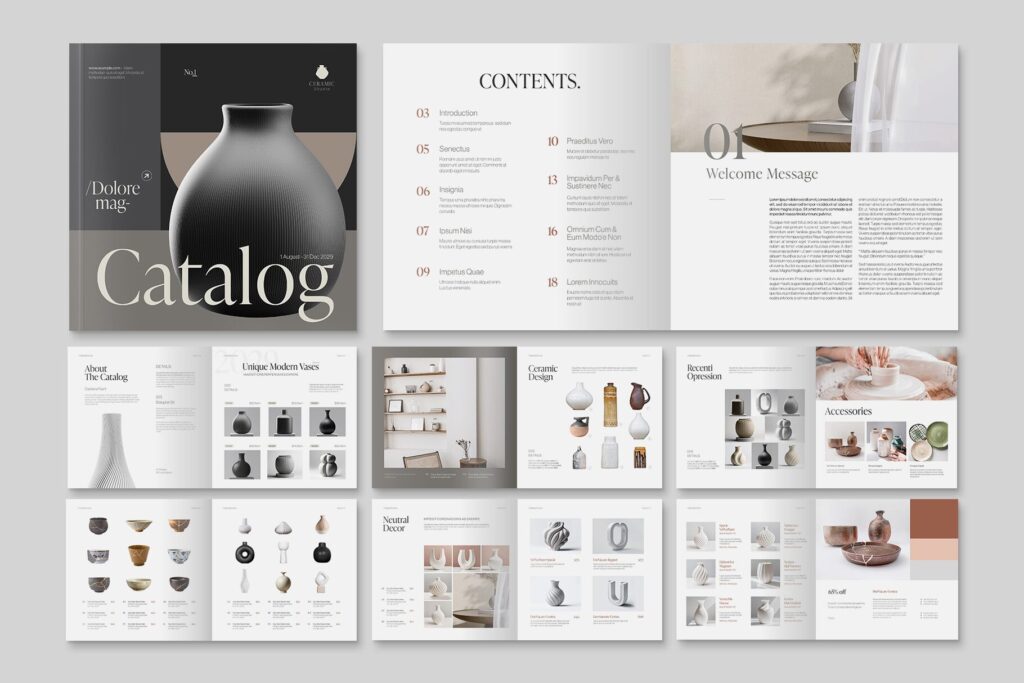
Offset printing is often the go-to method here because of its high speed, sharp image quality, and ability to handle large volumes at a low cost per unit.
✅ Popular in India for mass printing jobs in advertising, real estate, education, and political campaigns.
2. Packaging Printing
Another major application of printing presses is in the packaging industry. Today, packaging is not just about protection—it’s a key branding tool.
Common packaging items printed:
- Carton boxes
- Labels and stickers
- Corrugated boxes
- Bottle wraps
- Flexible packaging (like pouches)
Offset and flexo printing are widely used here. Many packaging jobs also include UV coating, lamination, and embossing for premium effects.
✅ India’s booming FMCG and pharma industries rely heavily on offset printing for packaging.
3. Book and Magazine Publishing
Books, newspapers, and magazines are still widely produced using printing presses, especially in bulk.
Used for printing:
- Textbooks
- Novels
- Magazines
- Comics
- Religious materials (like Bhagavad Gita or Bible copies)
- Academic journals
Offset printing handles large runs, while digital printing is great for short-run and print-on-demand jobs.
✅ Many Indian publishers still prefer offset printing for books due to better paper handling and print quality.
4. Newspaper Printing
Despite the rise of digital news, newspapers remain an important daily product for millions.
Printing presses are used to produce:
- Daily newspapers
- Weekly tabloids
- Local bulletins
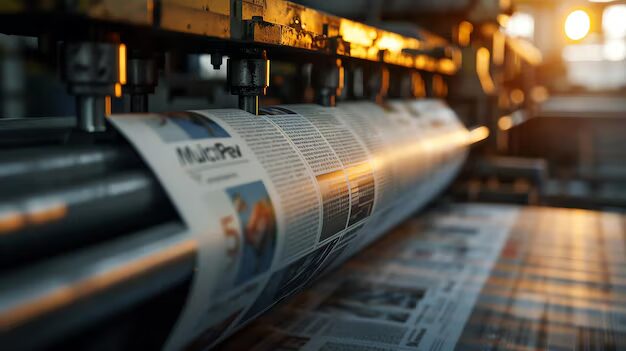
Web offset presses are the industry standard for printing newspapers. These high-speed machines use large rolls of paper and print both sides simultaneously.
✅ India has one of the world’s largest circulations of newspapers in multiple languages, making newspaper printing a major offset press application.
5. Label and Sticker Printing
From food packaging to electronics, labels are everywhere. Label printing presses produce:
- Barcode labels
- Product labels
- Hologram stickers
- Security tags
- Decorative decals
Digital label presses offer variable data printing, ideal for unique codes and QR codes.
✅ With the rise of e-commerce in India, demand for printed shipping and product labels has skyrocketed.
6. Advertising and Promotional Printing
Eye-catching prints help brands grab attention in crowded markets.
Printed items include:
- Standee displays
- Banners (vinyl and flex)
- POP/POS materials (Point of Purchase/Sale)
- Catalogs and product sheets
- Calendars
- Gift vouchers and coupons
Offset presses provide rich color and sharp details, while large-format digital printers are used for posters and billboards.
7. Textile and Garment Printing
Though screen printing is commonly used in fashion, digital and sublimation printing are growing rapidly.
Used for:
- T-shirt designs
- Fabric patterns
- Garment labels
- Bedsheets and scarves
✅ Textile hubs like Surat, Ludhiana, and Tirupur in India use a mix of digital and traditional presses.
8. Stationery and Office Supplies
Printing presses also support the production of customized or branded stationery:
Examples:
- Diaries and planners
- Notebooks
- Envelopes
- File folders
- Invoices and bill books
✅ These items are often printed in bulk for schools, corporations, and government offices using offset machines.
9. Security and Government Printing
Highly specialized presses are used for printing:
- Currency notes
- Stamps
- Bonds and share certificates
- Government IDs and forms
- Examination papers
These require secure offset or intaglio presses, with anti-counterfeit features like micro text, UV inks, and watermarks.
✅ The Government of India uses printing presses under its Ministry of Finance for official documentation.
10. Photobooks and Personalized Gifts
Digital printing has opened doors for short-run, customized printing.
Examples:
- Wedding albums
- Personalized calendars
- Custom mugs and T-shirts
- Greeting cards
- Photo books
✅ Urban print shops in cities like Delhi, Mumbai, and Bangalore offer same-day custom printing services using digital presses.
From newspapers to food packaging, the printing press process powers nearly every aspect of our daily lives. Its applications are vast and evolving with technology. Whether you’re a small business or a large industrial printer, understanding these uses helps in choosing the right printing method for your needs.
Common Applications of Printing Presses:
- Commercial print jobs
- Packaging and labels
- Books and magazines
- Newspapers
- Promotional materials
- Textiles and stationery
- Security and government prints
- Personalized gifts
The next time you hold a printed brochure, a milk carton, or a business card—remember that it all started with a printing press!
Conclusion
The printing press process may seem complex at first, but it plays a powerful role in everyday life, from the books we read and the packages we open to the posters we see around town. Whether it’s traditional offset printing or fast and flexible digital printing, the process is built on precision, creativity, and quality control.
Each stage—design, plate making, printing, finishing, and inspection—works together to bring ideas to life in vibrant color and sharp detail. With the right equipment, materials, and expertise, printers can produce everything from business cards and catalogs to packaging boxes and newspapers.
As technology continues to evolve, printing remains more relevant than ever, blending craftsmanship with modern automation. For businesses in India and around the world, understanding the printing process helps make better choices—whether you’re buying a press, managing a job, or launching a brand.
So next time you see a perfectly printed label or a glossy magazine, you’ll know the magic behind it. The printing press isn’t just about ink on paper—it’s about communication, creativity, and making a lasting impression.